Synchronous control solution for high-speed paper machine system
The control solution for the high-speed paper machine system with long-speed synchronization between batches (ice pressing, drying, optical pressing, coiling…) helps the system to operate stably, easy to operate, to produce quality products, increase machine efficiency, minimize waste and effectively save electricity.
Papermaking is the process of forming a paper structure and turning the pulp solution into a finished paper. The paper machine is a combination of many transmission parts and is divided into 2 parts: wet part and dry part.
The wet part is composed of powder injection box, mesh unit, stone press unit. The powder sprayer is responsible for evenly spraying the pulp solution onto the mesh. The newly formed paper is then passed through the stone press to squeeze out the water and increase the bond between the fibers.
The paper after passing through the wet part is still very moist (about 60%) will be dried to about 92% in the dry part, including pressing and drying rolls placed in series. In order to increase the quality and smoothness of the paper, at the end of the drying process there are also optical laminates. Finally, the finished paper will be rolled into large rolls by the roll collector.
Old-style operating method, machine parts are controlled separately for each batch.
CUSTOMERS’ DIFFICULTIES
- Easy to break paper, many waste products, uneven product quality
- Low machine speed, low production efficiency
- Almost no change in paper weight
- Difficult to adjust, difficult to paper and troubleshooting
- Regular maintenance of motors and mechanics affects production progress
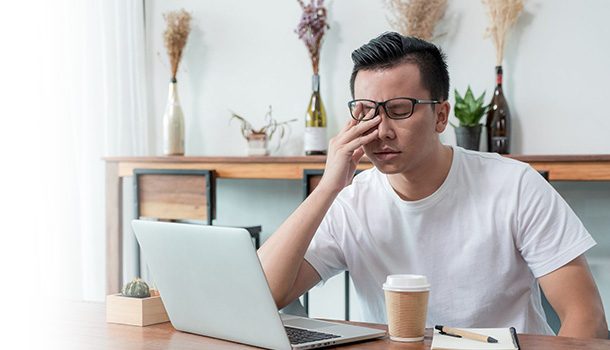
SOLUTION ANALYSIS
DAT provides 3 synchronous solutions and improves efficiency for paper machines:
- Solution 1: Synchronization solution using only GD200A inverter with machine speed < 100m/min, using analog control method or high frequency pulse link to synchronize the system in master-slave mode.
- Solution 2: Synchronous solution using open-loop inverter GD200A and PLC + HMI with machine speed up to 150m/min, using analog control method, high frequency pulse or communication according to Modbus, Profibus, etc. standards through PLC – HMI
- Solution 3: Synchronous solution using closed-loop inverters GD35/GD350 and PLC + HMI to control and monitor with machine speed up to > 200m/min, use communication such as Modbus, network, etc. precise control with 0.02% error
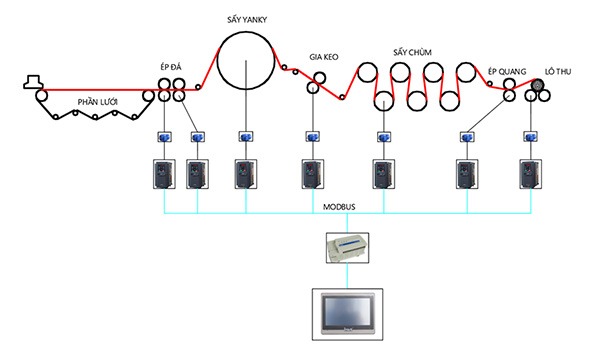
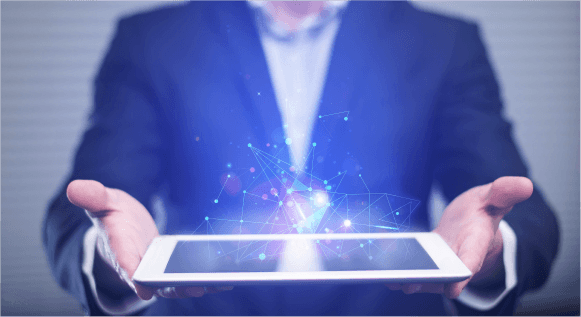
SOLUTION ADVANTAGES
- Synchronized system, easy to operate
- Avoid paper breakage, easy to troubleshoot
- Easily change machine speed and change paper weight
- Easy and intuitive parameter setting and monitoring using the HMI display
- Smooth start inverter, motor protection, mechanical shock resistance
- Complete solution, available warehouse, 24/7 service
Take a look at DAT's specialized solution design process.

Contact an expert
If you need advice and learn about DAT’s solutions, please contact 1800 6567 to meet with experts today.
Products for solutions
Solution relate:

10.000+

15+

3000+

24h
Let's go with DAT

24/7 SUPPORT

Hotline 1800 6567
