Solution to increase productivity and reduce waste for PP bag weaving machine
The solution of using INVT’s GD20/GD200A multi-function inverter to synchronously control the speed of the main motor system and the motors that pull the bag, pull the thread, and roll the bag, helps PP bag weaving machine operate stably, easily adjust and change orders, increase weaving speed, reduce waste and reduce machine downtime.
PP bag weaving machine uses PP yarn rolls to form PP film rolls before being coated and cut into finished bags for industries such as fertilizer, chemical, food, animal husbandry and many other fields.
The old operating method, weaving motors, thread traction motors and winding motors run directly on mains electricity and are independent of each other.
CUSTOMERS’ DIFFICULTIES
- The star-delta starter main motor causes mechanical shock, breaks the thread, greatly affects the needle, belt/belt, pulley, and bearing parts.
- The main motor runs at 1 speed, so the machine can only meet a few products
- Thread pulling motor and bag pulling motor run independently, so it is difficult to adjust the machine, depending on the operator’s experience
- Time consuming and costly maintenance
- The coil motor runs independently of the main motor, so the PP bag rolls unevenly. Low product quality, a lot of waste products
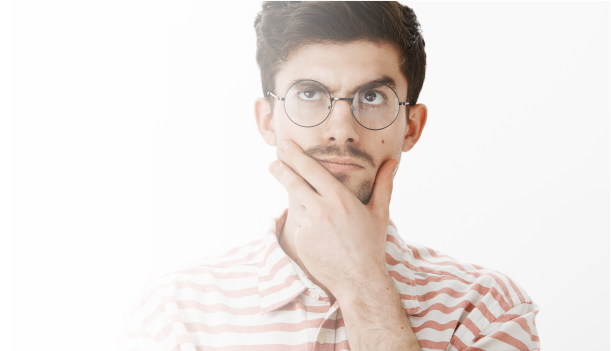
SOLUTION ANALYSIS
Using GD20/GD200A inverter to control main motor, bag traction motor, thread traction motor and winding motor, the inverters are synchronized with each other.
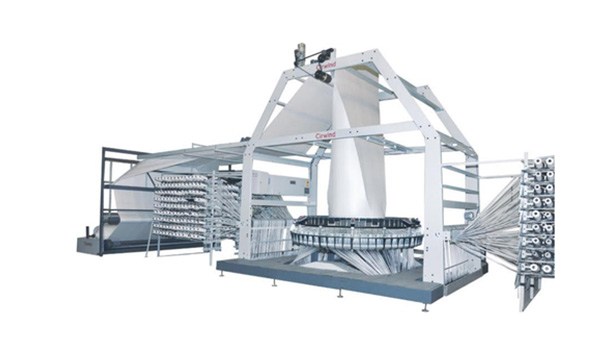
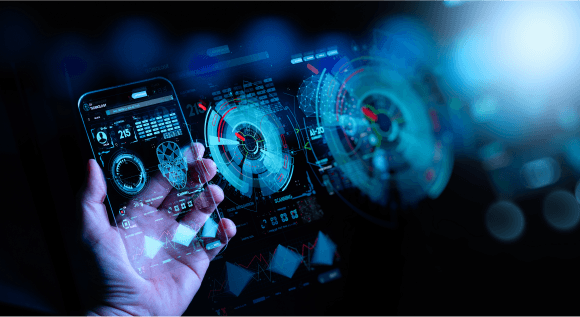
SOLUTION ADVANTAGES
- Synchronized system, easy to operate
- Improve productivity and product quality
- Reduce maintenance time, maintenance
- Engine protection, mechanical shock resistance
- Saving energy by adjusting the motor speed to the required load
- Complete solution, quick and easy installation. 24/7 service
Take a look at DAT's specialized solution design process.

Contact an expert
If you need advice and learn about DAT’s solutions, please contact 1800 6567 to meet with experts today.
Products for solutions
Solution relate:

10.000+

15+

3000+

24h
Let's go with DAT

24/7 SUPPORT

Hotline 1800 6567
