Solutions to improve efficiency and save energy for fabric tensioners
Using INVT’s PLC and multi-function inverter for the control solution of the needle tensioner system to help the machine system operate stably, improve the engine’s durability and save up to 10% of electricity consumption for the business owner. Karma.
The needle tensioner is a terminal device in a textile dyeing factory, which has the function of helping to stretch the fabric to the correct size, treat the shrinkage, create surface aesthetics and can adjust the weight of the finished fabric within certain. Mostly, the needle tensioner system is controlled by a dedicated controller according to the machine, the fan motor starts directly from the grid and always runs at a fixed speed at maximum capacity.
CUSTOMERS’ DIFFICULTIES
- Difficult operating system
- When there is a problem, it usually takes a long time to repair and there is no stock to replace
- Some machines are imported from Japanese yards, using 3P 220V power inverters that are not suitable for the power grid in Vietnam.
- The motor operates at full capacity continuously, consuming a lot of power
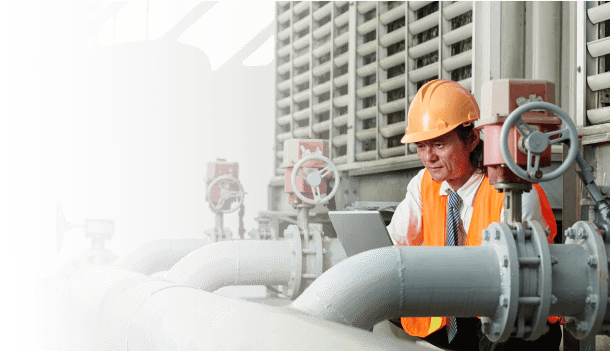
SOLUTION ANALYSIS
- Using INVT’s GD20/GD200A inverter to control batch speed and fan system flexibly according to operating requirements
- PLC synchronizes the system speed, ensuring the system always operates smoothly and efficiently
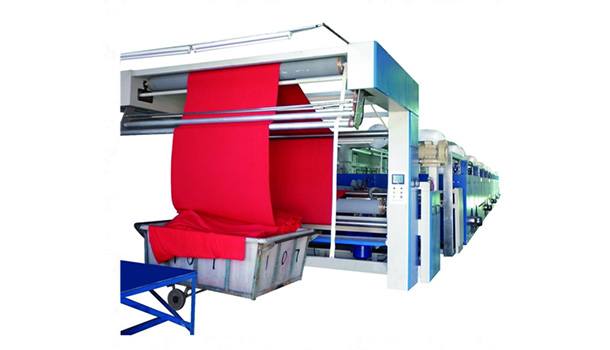
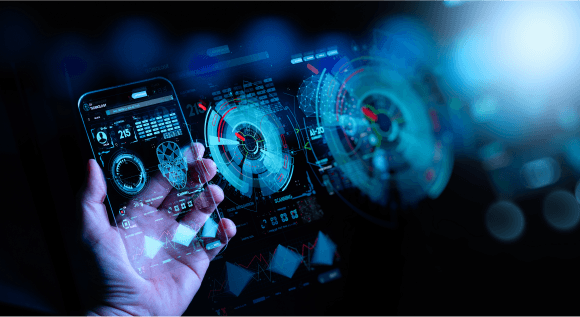
SOLUTION ADVANTAGES
- Simple machine operation, easy to change the motor speed to suit each fabric
- Improve technology suitable for national grid
- Reduce damage, improve product quality
- Smooth start, reduce mechanical wear, improve engine life
- Save 10% power consumption
- Giải pháp trọn bộ, lắp đặt nhanh chóng, dễ dàng. Dịch vụ 24/7
Take a look at DAT's specialized solution design process.

Contact an expert
If you need advice and learn about DAT’s solutions, please contact 1800 6567 to meet with experts today.
Products for solutions
Solution relate:

10.000+

15+

3000+

24h
Let's go with DAT

24/7 SUPPORT

Hotline 1800 6567
