VFDs for Air Compressor
Nowadays, with the development of science and technology, especially automation technology, many solutions have been created to easily solve control problems for air compressors. Among these, the inverter solution for air compressors is the most effective option to save energy and bring many benefits to businesses.
1. Inverter for Air Compressors
Air compressors are used to compress air to a certain value higher than atmospheric pressure. The types of air compressors widely used in industry include:
- Piston air compressors: These rely on the reciprocating action of one or more pistons to compress air inside a cylinder (or cylinders) and discharge it through a valve into high-pressure storage tanks.
- Screw air compressors: This type uses a volume mechanism where two helical screws rotate in opposite directions to change the air volume and generate air pressure.
- Centrifugal air compressors: These use high-speed impellers similar to those in pumps to impart velocity to the air, thereby increasing pressure.
The main applications of air compressors include creating compressed air to clear pipelines in wastewater systems, transporting goods, and controlling industrial manufacturing machines.
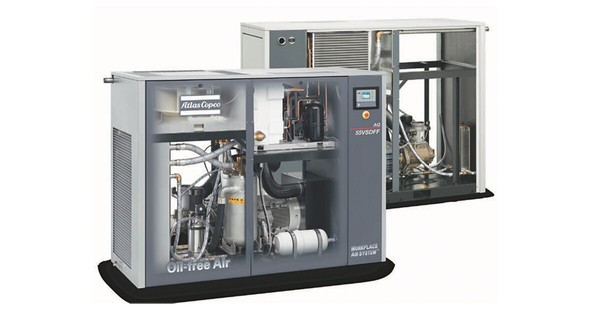
Air compressors typically require a large amount of electrical energy, making energy savings a very important aspect of their operation. Additionally, air compressors need to be stable and have high mechanical durability because repairs and maintenance are relatively costly and time-consuming.
2. Advantages of Using Inverters for Air Compressors
The advantages of using inverters for air compressors include:
- Flexible speed adjustment of the compressor to match load demands (energy-saving feature).
- Protection and extended lifespan of mechanical systems and motors.
- Improved power quality.
- Smooth start and stop processes, reducing compressor noise.
3. Benefits for Businesses When Using Inverters for Air Compressors
Air compressors operate continuously throughout the day, making it essential to use inverters for controlling them. During production, air compressors operate in two modes: LOADED and UNLOADED. The two-speed motor control method (star-delta) results in wasted electricity in the unloaded mode. Using an inverter for air compressors will automatically adjust the speed based on the loaded/unloaded mode, ensuring adequate air pressure for production while saving electricity. It reduces starting and unloaded currents, avoiding voltage drops that could affect other devices in the electrical network.
4. Ways to Maximize the Efficiency of Inverters for Air Compressors
Method 1: Reduce Starting Current and Consumption in Unloaded Mode
The inverter helps the air compressor start smoothly, reducing the rotation speed to a minimum and lowering consumption in unloaded mode, ensuring that oil is circulated to lubrication points.
Method 2: Control Air Compressor Flow According to Load Demand by Adjusting Motor Speed
The inverter adjusts the motor speed to maintain stable flow and pressure according to actual usage needs. Instead of a pressure range of 4-8 bar, this method maintains a 7 bar pressure by changing the motor speed. In most cases, the air compressor does not operate in unloaded mode.
5. Energy Saving Principle When Using Inverters for Air Compressors
Based on fluid/gas mechanics theory, the energy formula is:
P = K * Q * H
Where: P: Energy of the fluid/gas (kW)
H: Pressure (Pa)
Q: Flow rate (m3/s)
K: Constant
For fan load, the relationship between shaft power, pressure, flow rate, and motor shaft speed is:
Q1/Q2 = N1/N2 (1*)
H1/H2 = (N1/N2)² (2*)
From (1*) and (2*), we derive:
P1/P2 = (N1/N2)3 (3*)
Where: N: Motor shaft speed (rpm)
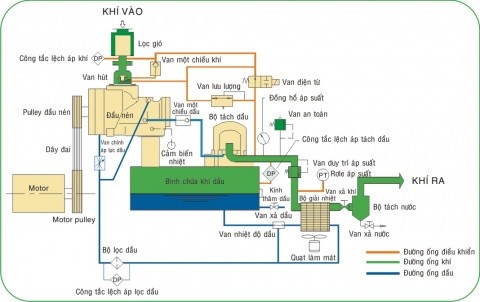
Assuming the motor speed is reduced by 50% of the nominal speed, the changes are:
- Flow rate in the pipeline decreases by 50%
- Air pressure in the pipeline decreases by (50%)²
- Motor power consumption decreases by (50%)³
6. Notes and Methods for Installing Inverters for Air Compressors
- The selected inverter should be for heavy-duty loads and have a fast response speed. Do not choose pump/fan-specific inverters with one power level increase, as their response capability is not high.
- When installing an inverter for an air compressor, consider the motor’s minimum speed. Motors without forced cooling fans may overheat if run at too low a frequency due to inadequate cooling.
- Running at too low a speed for extended periods or prolonged unloaded operation can lower the oil temperature, causing condensation and damaging the oil and other components.
- To write an optimal inverter control program, understand the structure and operation of air intake and oil intake valves and protection signals.
7. Recommended Inverters for Air Compressors
Current inverter products DAT is applying for air compressors include:
- INVT Brand
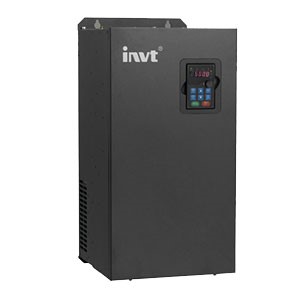
- Hãng SIEMENS
DAT Technology Co., Ltd. is a leading provider of products and solutions in the fields of automation, solar power – energy storage, elevator control, and UPS in the Vietnamese market.
With over 15 years of development and a value ecosystem, DAT has gained the trust and cooperation of over 10,000 customers and partners nationwide.
DAT is the general representative of INVT and an official distributor of Siemens in Vietnam, offering a wide range of high-quality INVT and Siemens inverters that meet all specialized customer requirements. When purchasing from DAT, customers are assured of:
- 12-24 month warranty.
- Lifetime maintenance.
- 24/7 engineer support.
- Flexible payment and pre-shipment delivery.
Contact our toll-free hotline 1800 6567 or chat with a consultant via the chat box in the bottom right corner of the screen. DAT is always ready to support you!