Solutions to Enhance Efficiency for the Paper and Paper Packaging Industry
The paper and paper packaging manufacturing industry is thriving with an annual growth rate of 15-18%, presenting many opportunities as well as challenges for businesses in the sector. The key issue is how to innovate technology, enhance efficiency, improve product quality, and optimize costs to increase competitiveness in the market, especially in the export market, which remains a challenging problem for Vietnamese paper companies.
Technological Challenges
Vietnam’s paper and paper packaging industry has many advantages due to its abundant raw materials and proximity to the world’s largest pulp consumer market, China.
However, fierce competition in both the domestic and export markets poses significant challenges for the Vietnamese paper industry. The lack of competitiveness compared to regional rivals largely stems from technological limitations such as low precision, slow machine speeds, low production efficiency, difficult operation and error handling, and high maintenance and motor repair costs.
Moreover, the paper and paper packaging industry is one of the most energy-consuming sectors, with energy costs accounting for 20-40% of the product price. Therefore, finding solutions to innovate technology, improve production efficiency, and save energy is an urgent need for paper enterprises.
Implementing Automation Technology to Solve Industry Problems
To optimize performance, enhance product quality, and save costs, machinery systems in paper and paper packaging factories need to operate efficiently and stably for extended periods. The application of automation technologies aimed at improving equipment and enhancing operational capabilities is chosen by many factories to overcome current difficulties.
Several successful solutions have been implemented in many paper and carton packaging factories:
- Installing Inverters for Motor Speed Control to Innovate Technology, Optimize Efficiency, and Save Energy:
Inverters are very common in electrical and automation systems, used to change the frequency of the power supply, thereby altering the motor speed. The advent of inverters helps paper mills innovate technology, optimize efficiency, and save energy. In some specific applications, using inverters can help factories save 30-40% of electricity.
Some positions in paper and carton packaging factories where inverters can be installed include:
- Wood chippers
- Hydraulic grinders
- Paper machines
- Air compressors
- Pump and multi-pump systems
- Boilers
- Rewinders
- Corrugating and slitting systems for carton paper
- Printing and die-cutting machine control systems
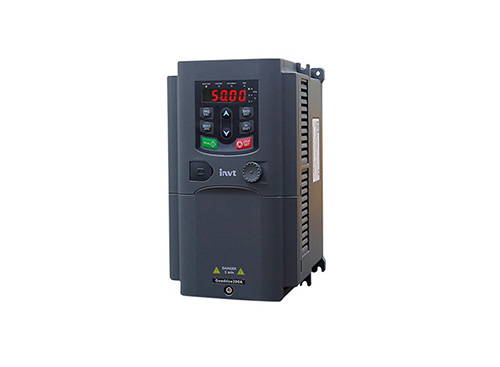
2. Synchronized Control Solution for High-Speed Paper Machines:
For paper production factories, the paper machine system is crucial, determining the quality of the paper. Factories using old technology with individually controlled rollers face difficulties in operation, affecting product quality and reducing production efficiency.
Challenges include frequent paper breaks during production:
- High scrap rates
- Low machine speeds
- Difficulty in adjusting when changing weight
- Complicated operation and error handling
- High maintenance costs for motors and mechanics.
The high-speed paper machine synchronization solution helps synchronize the speed of the long rollers (press rolls, drying rolls, glossing rolls, winding rolls, etc.). The solution uses inverters and PLC, HMI programming units. Depending on the speed and power levels, factories can choose from 3 solutions :
- Synchronized control using only inverters for machine speeds <150m/min.
- Synchronized control using open-loop inverters and PLC + HMI for machine speeds up to 150m/min.
- Synchronized control using closed-loop inverters and PLC + HMI for machine speeds up to 300m/min.
3. GD35-09 Synchronized Control Cabinet Solution for High-Speed Rotary Knife Cutting Machines in Carton Packaging Factories:
The rotary knife cutting machine is the heart of carton paper factories. Traditional solutions using mechanical CAM systems, specialized control cabinets, or PLC combined with inverters cause significant difficulties for factories.
Challenges:
- Large errors
- High scrap rates during cutting
- Low machine speeds, unstable systems
- Poor cut quality
- Extended machine downtime, slow repair times due to lack of timely support
- Dependency on specific suppliers and specialized engineers.
The synchronized control solution for rotary knife cutting machines requires a highly complex control level, with few domestic units able to meet the demand. The GD35-09 integrated control cabinet solution for high-speed rotary knives helps customers operate and control orders easily, increase productivity, speed, and product quality, and eliminate scrap.
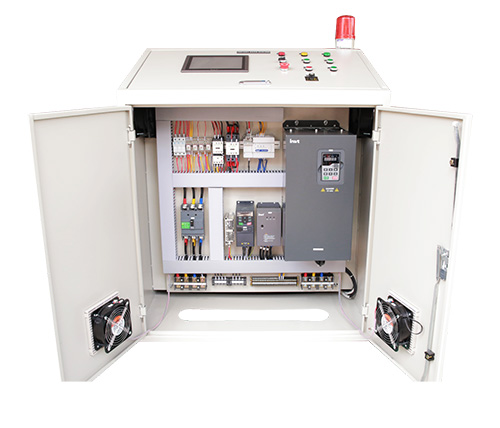
DAT – 15 Years of Developing Automation Solutions for the Paper and Paper Packaging Industry
With a team of experienced engineers and 15 years of industry knowledge, DAT and INVT have researched and provided the most effective solutions to meet the needs of paper industry customers. DAT has successfully supplied and received satisfaction from many customers in the paper industry, such as Tan Thanh Dong Packaging Company, Duong Nguyen Paper Packaging Co., Ltd., Xuan Mai Paper Co., Ltd., Công ty TNHH Thương mại Sản xuất Giấy Đồng Phú…
BENEFITS OF DAT’S SOLUTIONS:
- Technological innovation, improved product quality.
- Increased machine efficiency and speed, boosting production productivity.
- Easy operation, reduced scrap.
- Stable machinery operation, motor protection, reduced downtime, and maintenance costs.
- Energy savings.
Conclusion
To sustain and develop, the paper and paper packaging industry must take comprehensive measures to leverage opportunities and strengths, overcome difficulties and challenges. With DAT’s solutions, Vietnamese paper companies can invest in production lines, easily and effectively modernize technology, save costs, and confidently compete with other countries in the region.