High-speed centrifugal extractor control solution for textile dyeing industry
Using INVT’s new generation multi-function inverter GD200A to control the high-speed centrifugal extractor helps the system operate smoothly, avoid shaking, shorten the drying process, save time and improve production efficiency.
Centrifugal extractor is an important equipment in many different production stages in industrial fields such as yarn, fabric, textile and dyeing, medical, food, etc. used to separate water by spinning, creating a large centrifugal force meets operator’s requirements. The old-style control method, the centrifugal extractor is started in star, delta and mechanical brake is used to stop the motor.
CUSTOMERS’ DIFFICULTIES
- The large starting current causes a voltage drop on the plant power line.
- Instant start causes mechanical shock, sinificantly affecting belts, pulleys, bearings, etc.
- Using mechanical brakes is very easy to wear and tear, frequent maintenance and replacement.
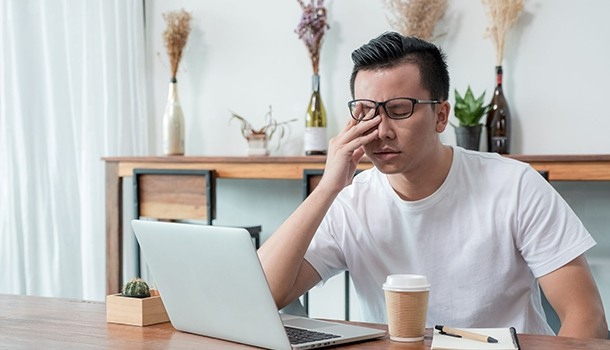
SOLUTION ANALYSIS
DAT offers a solution to control the high-speed centrifugal extractor by installing the INVT GD200A universal inverter for the extractor motor. The system uses a DBU dynamic brake (built into the inverter below 37 kW) combined with a discharge resistor to brake the motor.
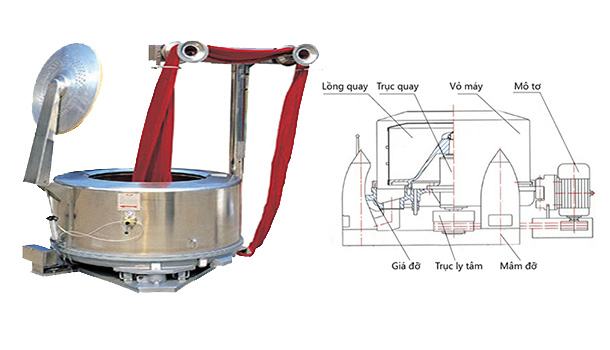
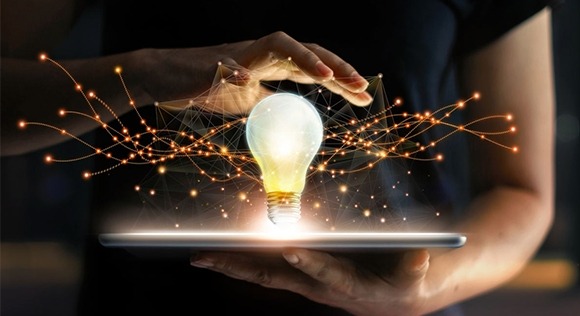
WHAT CAN DAT HELP YOU
- Set the operating time of the extractor using the timer available in the inverter
- The speed can be easily adjusted according to each product
- Smooth start and stop, minimize vibration
- Easy to operate with simple interface
- Save energy with products that need low speed
- Complete solution, quick and easy installation. 24/7 service
Take a look at DAT's specialized solution design process.
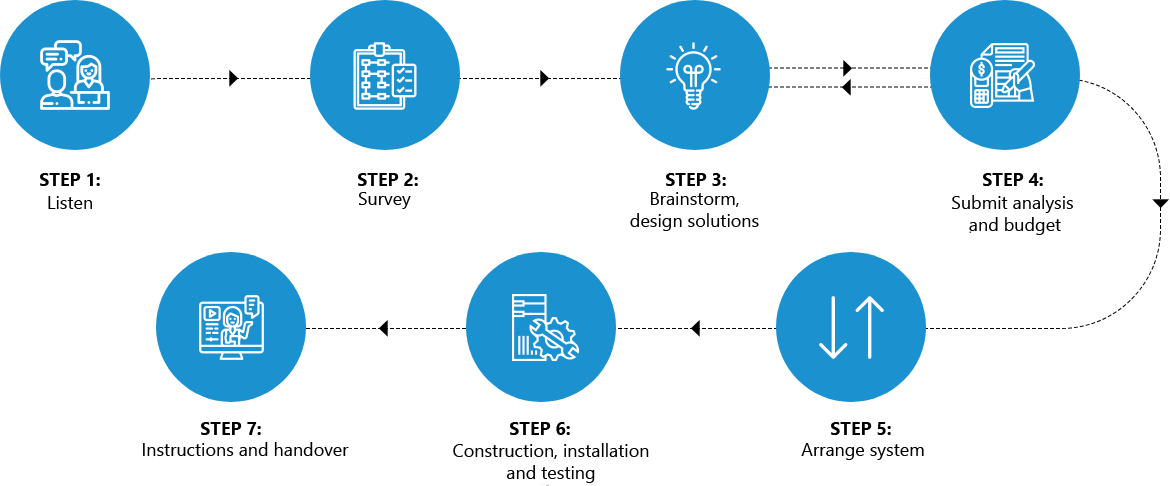
Contact an expert
If you need advice and learn about DAT’s solutions, please contact 1800 6567 to meet with experts today.
Products for solutions
Solution relate:

10.000+

15+

3000+

24h
Let's go with DAT

24/7 SUPPORT

Hotline 1800 6567
