Differences between VFD and servo drives
Choosing between a servo system or using a three-phase motor controlled by a VFD in specific applications is a question that often leaves many machine designers and engineers in a dilemma during the design and construction of machinery. Understanding the differences between a VFD and a servo motor controller (servo drive) will help engineers make the most optimal choice.
In the past, the application scope of servo motors and asynchronous three-phase AC motors was distinct. Three-phase AC motors were used in applications with high power requirements such as air compressors, pumps, fans, heavy-duty conveyors, etc. On the other hand, servo motors were employed in applications with low power, high torque, high precision position control, and continuous operation at constant torque, such as CNC machines, robots, machine tools, and pick-and-place applications.
Today, with the continuous development of VFD technology, the application scope of three-phase motors has expanded. With the ability to change speed smoothly and various control capabilities, three-phase motors (especially when combined with VFDs) can now replace some applications traditionally exclusive to servo systems. So, how do VFDs and servo motor controllers differ?
VFDs and Basic Applications
A VFD is known for altering the frequency of the current supplied to the coils inside a motor, thus enabling the control of motor speed smoothly. VFDs are commonly used to control three-phase asynchronous AC motors. However, modern technology has allowed certain VFDs to control not only asynchronous motors but also synchronous motors, spindle motors, and even servo motors.
Benefits and basic applications of VFDs:
- Control motor speed to meet basic industrial production requirements.
- Facilitate smooth motor startups, reducing mechanical wear.
- Effectively save energy, protecting system components.
- Incorporate various control functions to enhance technology and production efficiency.
- Include protective functions for motors, such as overcurrent, overvoltage, phase loss, and phase reversal, contributing to motor longevity.
Servo Systems and Servo Drive
A servo system is a closed-loop control drive system that receives pulse signals and rapidly and accurately executes commands from a PLC. A servo system consists of a servo motor controller, a servo motor, and an encoder mounted on the motor shaft to provide continuous feedback on the motor’s current position and speed.
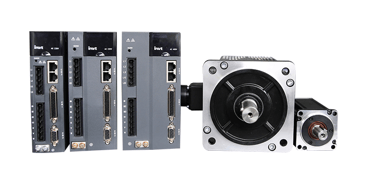
The servo motor controller’s role is to receive control signals (pulses) from the PLC, transmit commands to the servo motor to control its operation according to the instructions, and simultaneously receive continuous feedback signals on the motor’s current position and speed from the encoder. Based on the feedback signals, the servo motor controller compares them with the control signals and adjusts accordingly, ensuring the servo motor operates precisely as required.
The servo system is used to start and stop at precise positions down to micrometers, adjust torque according to different applications, and achieve extremely fast speed changes down to milliseconds.
Applications of Servo Systems:
Servo systems are commonly used in applications requiring extremely high precision in position, speed, and torque, as well as complex control capabilities, high-speed operation, and rapid and continuous changes in operation, such as CNC machines, packaging machines, various types of printers, cutting machines, roll-fed applications, stop-and-go applications, assembly lines, CNC machines, and robotic arms…
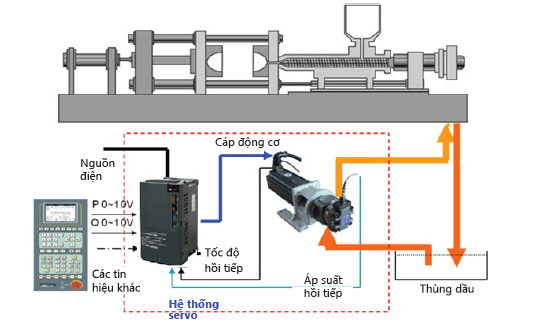
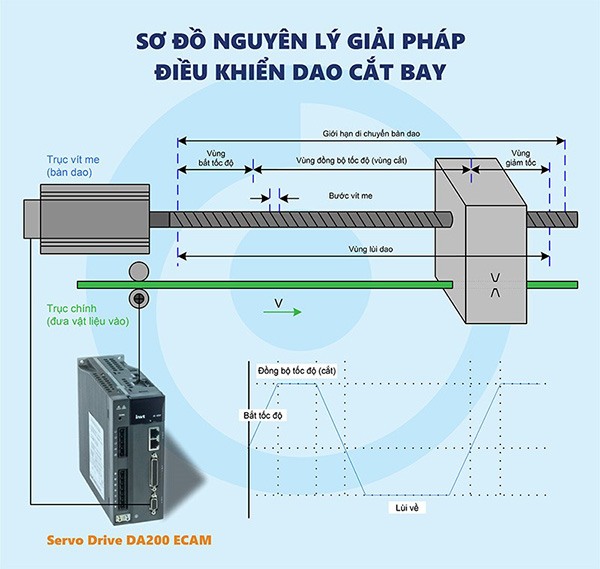
When to Use VFDs and Servo Motor Controllers
In essence, servo controllers and VFDs are devices used to control motors. However, while servo controllers can precisely control speed, position, and torque, VFDs, despite being upgraded with additional features, fundamentally rely on changing the frequency to control motor speed. In terms of control quality and precision, servo controllers outperform VFDs. VFDs are typically used in cases with low precision requirements, stable operating speeds, and minimal variations. However, VFDs are cost-effective and can control various types of motors without being limited to a single servo motor.
To make the most optimal choice, refer to the comparison table between VFDs and servo controllers below:
VFDs | Servo Drives | |
---|---|---|
Control Application | Used in applications with low precision, stable speed, and minimal variation | Used in applications requiring high precision in position, speed, and torque, with rapid and continuous changes |
Control Modes | Primarily controls motor speed | Controls position, speed, and torque |
Control of Multiple Motors | Can control multiple motors | Typically controls a single servo motor |
Response Time | Slow 100 rad/second or lower |
Fast Range from 200 to 15,000 rad/second |
Positioning Accuracy | About 100 µm | Up to about 1 µm |
Locking Mode | No | Yes |
Start/Stop Frequency Range | About 20 revolutions/minute or lower | About 20 to 600 revolutions/minute |
Maximum Torque | About 150% | About 300% |
Power | About 100W to 300kW | About 10W to 60kW |
Size | Larger and heavier | Smaller and lighter (with the same power) |
Investment Cost | Relatively low | High |
To make the most optimal choice, the decision between a variable frequency drive (along with a three-phase motor) and a servo motor controller (servo system) will depend on the specific application, system requirements, and overall cost (both initial investment and the system’s lifecycle cost). Choosing the wrong product can result in the machine system not achieving the desired technological and efficiency goals, leading to waste and potential impact on other related equipment.
In some cases, if a servo motor controller fails while the servo motor is still operational, to save costs, some specific variable frequency drives (such as GD35, GD350) can be used as replacements for the servo motor controller to control the servo motor. This option, however, depends on the specific system and should only be considered when the cost of replacing the servo drive is excessively high, delivery time constraints affect production schedules, or when it is not possible to source a replacement from the supplier.
For the most suitable and effective solutions for your application, contact DAT’s experts via the hotline 1800 6567.