Solutions for using inverters for livestock farm ventilation systems
In livestock farms, the ventilation system plays a central role in determining the growth of animals. A standard ventilation system will help remove moisture, odors, dust, pathogenic microorganisms; supply and uniform distribution of clean air; ensure cool temperature in summer, warm in winter.
Currently, most of the medium-sized and larger farms use a system consisting of many industrial fans combined with other auxiliary components such as misting systems, cooling systems, etc. to ventilate. However, this system still has many limitations that make farmers have to look for a new, more optimal method.
OLD METHOD OF VENTILATION WITH INDUSTRIAL FANS
Principle of operation
With the closed barn design, when the fan works, it will suck the air inside the barn out, creating negative pressure in the barn. This negative pressure will draw air into the barn through the cooler. The larger the amount of air sucked through the blower, the higher the negative pressure will be and the more air will be drawn into the barn. Therefore, it is possible to control the temperature and humidity factors in the barn by controlling the wind speed, or more precisely, controlling the working capacity of the blower in combination with the operation of the cooling rig at the top of the barn (cooling 1) and the cooling system inside the barn (cooling 2).
LIMITATIONS OF THE SOLUTION
The fan system works manually, starting directly with the mains power and ON – OFF according to the experience of the farm operator. Accordingly, the operator starts many fans when the temperature is high and gradually decreases when the temperature is low. This causes many problems such as:
- Operating according to experience, temperature and humidity are not guaranteed to be adjusted accurately and timely, affecting animal health
- Direct starting system causes mains voltage drop, easy to burn, reduce fan life
- The fan motor when operating always runs at full capacity regardless of the reduced demand in the evening, cold season, etc., causing power loss.
- It takes time and manpower to check regularly due to manual operation.
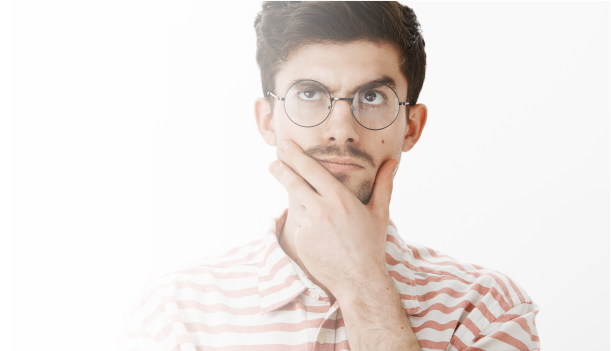
USING GD200A INVERTER TO CONTROL FAN SYSTEM
Facing many limitations of the old operating method, many farm owners have chosen to use the GD200A inverter in combination with a temperature sensor to control the fan system.
The sensor is installed inside the barn to measure the temperature and output the signal to the inverter. When the temperature drops, the inverter drives the fan to operate at a low speed. When the temperature rises, the inverter controls the fan to increase the speed accordingly to ensure the most suitable temperature in the barn.
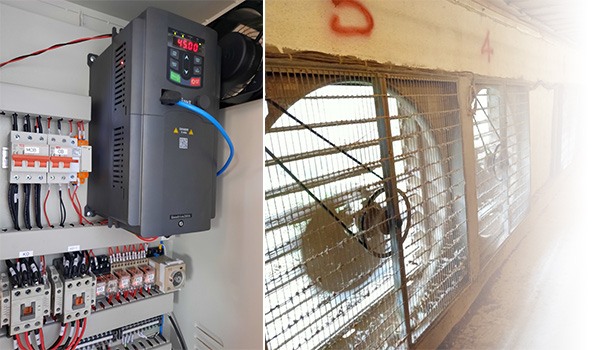
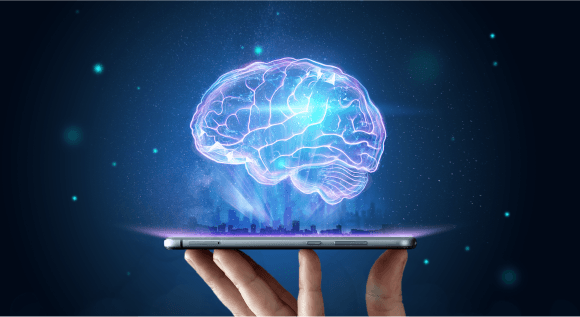
SOLUTION ADVANTAGES
- Always ensure the right temperature inside the barn, ensure the health of the animals, especially those that are sensitive to the environment.
- Adjust the fan speed to operate according to the needs, helping to save energy.
- The system is automatic, independent of the operator.
- Motor soft start, avoid mains voltage drop, mechanical protection.
Take a look at DAT's specialized solution design process.

Contact an expert
If you need advice and learn about DAT’s solutions, please contact 1800 6567 to meet with experts today.
Products for solutions
Solution relate:

10.000+

15+

3000+

24h
Let's go with DAT

24/7 SUPPORT

Hotline 1800 6567
