Control solution for medical mask production machine
The solution to control the medical mask production machine using PLC/HMI and DA180 Servo of INVT helps to optimize control, improve the speed, productivity and efficiency of the machine, and stabilize the output product quality for the customer.
The medical mask production machine is complicatedly composed of many different parts such as and divided into 3 main parts: billet forming machine, billet flipping table, strap press.
- Billet forming machine: is responsible for creating the body of the mask from the filter cloth rolls and the nose clip coil. Machine productivity is close to 300 pieces/minute (actual speed depends on mechanical system). The performance of the machine depends on 2 factors: machine speed and ultrasonic welding technology.
- Billet flipping table: is responsible for turning the workpiece upside down, pushing the billet into the conveyor and feeding the billet to the strap press. The system normally has 1 or 2 billet flipping tables depending on the number of strap presses.
- The strap press is responsible for pressing 02 straps to the billet, the finished billet will be taken to the end of the conveyor and finished product shall be packaged.
Previously, most of the medical mask making machines were imported from China. After the outbreak of the Covid-19 epidemic, a number of domestic machine manufacturers have started researching to produce mask making machines to meet the domestic market, but the implementation is still difficult due to lack of understanding the complete technology, there is no optimal control solution, the machine speed is low and unstable.
CUSTOMERS’ DIFFICULTIES
- Low machine speed, inefficient productivity
- The speed is not synchronized from the billet forming machine to the billet turning table and the strap press, leading to excess work in the loop press when the bar forming machine is operating at too high speed or lack of billet, stopping the machine continuously when the billet forming machine is running in too low speed
- Product quality is not high, many waste products
- The system is unstable due to the interference from the ultrasonic welding machine’s high-frequency waves, greatly affecting the productivity and product quality.
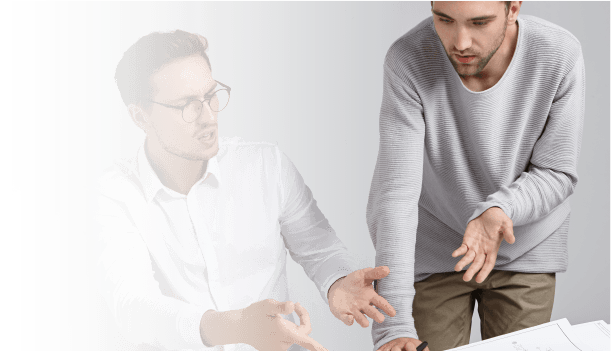
SOLUTION ANALYSIS
Solution using PLC IVC3, HMI VS and Servo DA180 with CANopen communication helps to solve all the above difficulties.
- Use the DA180 servo unit to precisely control the speed and position of conveyor mechanisms, billet conveyors, strap presses and cloth presses.
- PLC IVC3 controls the whole system and is monitored by HMI display. PLC IVC3 implements CANopen communication with 4 sets of AC Servo DA180s (integrated with CANopen communication standard). Then the position and speed of 4 servomotors will be configured in the memory area of the PLC to ensure very high machine speed and not be affected by the high frequency interference of the ultrasonic welding machine.
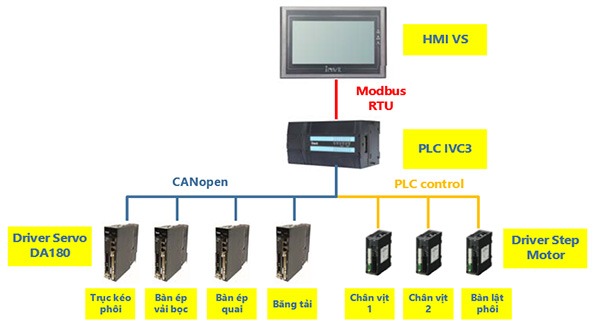
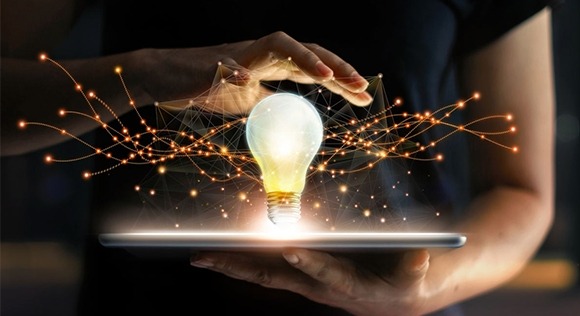
SOLUTION ADVANTAGES
- Machine high speed.
- Ensure speed synchronization between mechanisms and stages in production.
- Easy to control and operate the Vietnamese screen displays.
- CANopen communication enables fast data transmission, completely eliminates system interference caused by high frequency waves, increasing productivity and product quality.
- Complete solution, quick and easy installation. 24/7 service.
Take a look at DAT's specialized solution design process.

Contact an expert
If you need advice and learn about DAT’s solutions, please contact 1800 6567 to meet with experts today.
Products for solutions
Solution relate:

10.000+

15+

3000+

24h
Let's go with DAT

24/7 SUPPORT

Hotline 1800 6567
