What is Electronic Cam (ECAM)? Applications of ECAM in automation
The trend of automation in manufacturing witnesses a shift from older, low-performance technologies to newer, more advanced, flexible, precise, and high-performance technologies. In the past, some master-slave control systems like rotary cutters, flying cutters, and sawing machines used mechanical cam mechanisms, which were low-speed, low-precision, and required frequent adjustments and maintenance. However, nowadays, Electronic Cam (ECAM) technology can replace mechanical cam mechanisms, overcoming all the drawbacks of mechanical cam systems, significantly enhancing manufacturing efficiency.
So, what is Electronic Cam (ECAM)?
1. Mechanical Cam Mechanism
To understand ECAM, it’s essential to first learn about mechanical cam systems. A mechanical cam system comprises camshaft (master – driving element) and follower (slave – driven element) connected through joints. The cam mechanism is used to convert the rotary motion of the camshaft into linear or oscillatory motion in follower, with repetitive or cyclical behavior according to predefined pattern. The shape of the working surface of cam (cam profile) is designed to follow motion law. As camshaft rotates, follower moves linearly or oscillates in accordance with cam profile. Each position on camshaft corresponds to unique position of follower.
Mechanical cam systems are widely used due to their simplicity, high efficiency, cost-effectiveness, and few moving parts.
Drawbacks:
- High precision errors.
- Mechanical cam mechanisms often wear out and require frequent maintenance.
- When changing speed, the adjustment of stroke takes time.
2. Electronic Cam (ECAM)
Electronic Cam (ECAM) is a software algorithm typically integrated into control systems like PLCs, servo drives, or VFDs, based on the principle of simulating the cam profile to perform master-slave applications with repeatability or cyclical behavior, replacing the mechanical cam mechanisms. In other words, ECAM is a software component that calculates the correlation between the master axis or master encoder and the slave motor, where each position of the master (axis x) corresponds to a unique position of the slave (axis y), expressed through an ECAM parameter table.
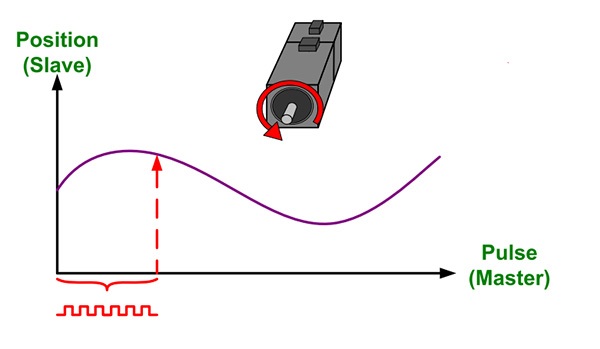
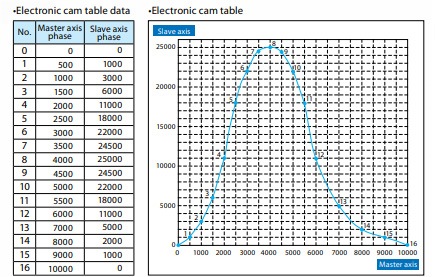
In addition to position control, the ECAM algorithm software allows for flexible adjustments of speed, acceleration, and time.
Benefits of ECAM:
- Precise, stable, and smooth control: Each position in operation cycle is expressed in ECAM table with high interpolation, ensuring extremely accurate and stable motion. Additionally, ECAM software supports interpolation between two points, enabling smoother operation.
- Fast and short cycle time: When using ECAM, each position (point) in the curve is accurately determined, ensuring fast response, minimal delay between states, and a significantly reduced cycle time.
- Easy adjustments: Unlike mechanical cams that require changes to cam profile or adjustments to camshaft positions when there are speed, time, or position changes during operation, ECAM can be easily adjusted by modifying data in Electronic Cam table (if position changes are needed). Speed and time can also be changed effortlessly and flexibly within the ECAM software.
- Minimal maintenance: The ECAM system avoids the use of mechanical components, eliminating wear and tear, resulting in reduced maintenance requirements. Calibration is straightforward and quick.
Applications of ECAM in industries:
ECAM is typically integrated into servo drives (or PLCs, VFDs) and used in master-slave control applications that demand responsiveness, precision, and high speed, such as rotary cutters, flying cutters, sawing machines, and more.
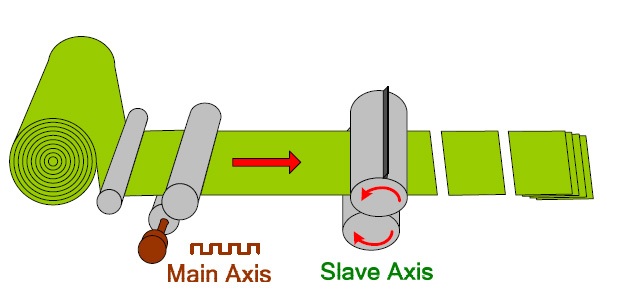
Example of solution using DA200 servo with integrated ECAM control for flying cutter:
The system utilizes the high-end DA200 Servo (INVT), which includes a control driver integrated with ECAM. The main axis (master) feeds material in, and servo motor is attached to lead screw to control cutter’s speed (slave). The closed-loop control mode and the servo’s quick response capability ensure that cutting motion is precise and accurate, following set position and length accurately. When material speed and cutting length change, system immediately adjusts motor speed to maintain precise position and stable speed, ensuring accuracy even at high cutting speeds.
DA200 Servo (INVT) with integrated ECAM – precise and flexible control for complex applications:
The INVT DA200 Servo, distributed by DAT, integrates ECAM with cam profiles of up to 1000 points, offering various benefits for customers:
- Extremely high synchronization, extremely accurate and stable position control, eliminating product defects entirely.
- Intelligent system operation with easy adjustment of multiple modes, convenient for order changes. Supports up to 10 orders.
- Maximizing cutting productivity by improving system speed, minimizing downtime.
- Supports interpolation between two points, providing smooth operation.
- Reduces maintenance, repairs, and premium control algorithms for smooth, vibration-free operation, and mechanical wear protection.
Ngoài ra DA200 còn có nhiều tính năng đặc biệt khác đáp ứng hoàn hảo yêu cầu điều khiển hiện đại:
- The wide power range from 0.1 kW to 55 kW
- The exceptional speed response with a response frequency of up to 2.0 kHz
- Outstanding position accuracy of ±0.01mm, 0.03% speed accuracy
- The full-closed-loop control mode
- It also supports various communication protocols such as Modbus, Profibus, EtherCAT, CANopen, Motionet
With these superior features and DAT’s professional, dedicated, and fast technical service, DAT commits to delivering the best efficiency for your factory operations. Contact us today to discover breakthrough solutions that increase profitability.