Function of VFD
With its superior utilities, inverters have now become an indispensable part of machinery systems, especially in the automation industry.
1. Changing motor speed to meet technological requirements
The working principle of the inverter relies on three main components: rectifier, filter, and inverter. Specifically:
- Rectifier: Converts single-phase or three-phase AC power into DC power (DC voltage) and stores it in a capacitor.
- Filter: Used to smooth out the DC voltage.
- Inverter: Applies Pulse Width Modulation (PWM) through an IGBT (Insulated Gate Bipolar Transistor) system to create symmetrical three-phase voltage.
The formula for calculating motor speed: N = (2x60xf)/P
F is the frequency of the voltage supplied to the motor.
P is the number of pole pairs in the motor.
Based on this working principle, the inverter adjusts the output frequency of the symmetrical three-phase voltage supplied to the motor, allowing the motor speed to be adjusted to meet technological requirements.
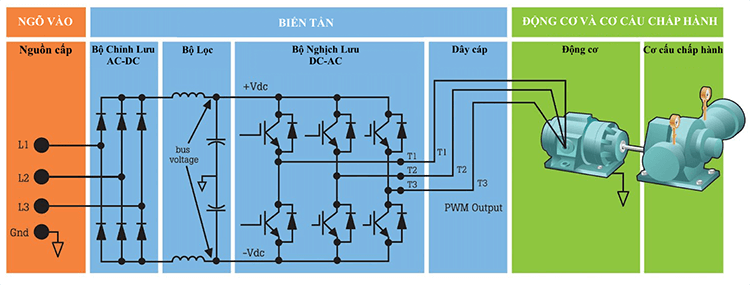
2. Protecting the motor and reducing mechanical wear
The inverter changes the motor speed from startup to rated speed, ensuring that the startup current does not exceed 1.5 times that of star-delta starting and 4-6 times that of direct starting.
The inverter integrates functions for overload, overcurrent, overvoltage, and undervoltage protection, helping to protect and extend the motor’s lifespan.
The inverter smooths the motor startup process, avoiding shocks and reducing mechanical wear.
3. Energy saving
Compared to direct starting, the startup current using an inverter is reduced by 4-6 times, thus reducing energy consumption by 20-30%.
Moreover, for applications such as pump control, fans, compressors, and other applications requiring flow or pressure control, the inverter will reduce/stop the motor in no-load conditions, thereby maximizing energy savings.
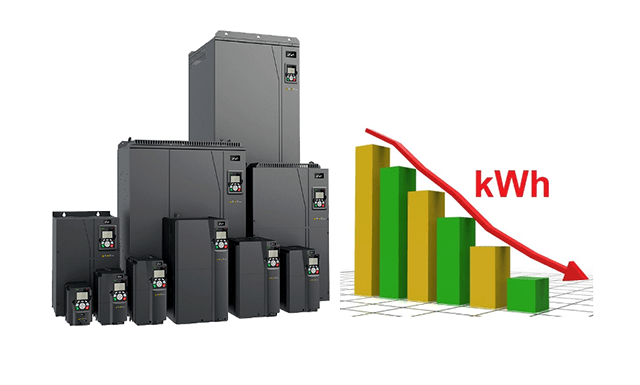