Q&A
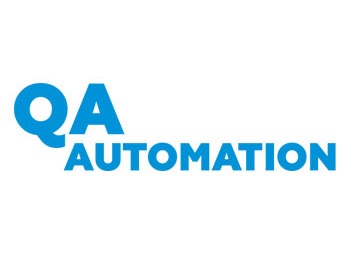
Why does turning on circuit breaker for VFD not make motor run?
The following reasons may cause this issue: The circuit breaker is faulty and not supplying power to VFD. The VFD has not received a run command or run command has not been configured. The VFD is indicating an error. How to address these causes: Check the power supply to VFD. Verify if there is a ... Read moreQ&A
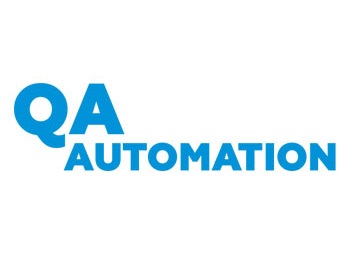
Why does increasing potentiometer resistance result in a decrease in VFD’s output frequency?
The reason for this situation is that potentiometer may be wired incorrectly or corresponding Analog value setting is not proportionate. Please change the wiring order of potentiometer GND ±10V and review settings in parameter group P5.
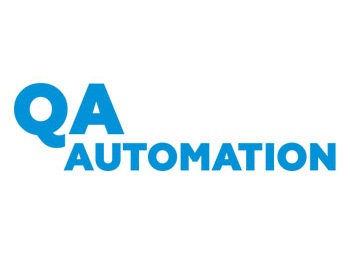
Why can’t VFD accelerate/decelerate when it is running, using the keypad?
In this case, the following situations may occur: The UP/DOWN function is disabled The buttons are stuck or the keypad cable is disconnected The motor is mechanically blocked or damaged The output current of VFD reaches the protection threshold Troubleshooting steps: Enable the UP/DOWN function via the keypad Resolve any mechanical load blockage before attempting ... Read moreQ&A
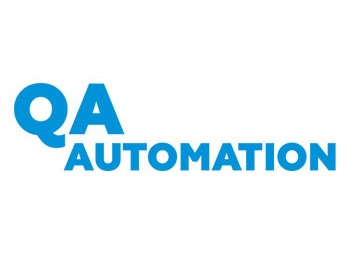
Why doesn’t VFD accelerate when there is a load?
The reason for this situation may be due to an excessively heavy load or a mechanical blockage causing a high output current. In the control algorithm of VFD, if the output current exceeds the rated level, VFD will automatically reduce the output frequency. Additionally, it is important to check the motor connections and the V/F ... Read moreQ&A
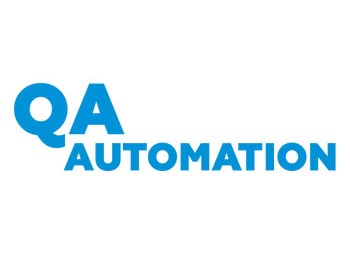
Can a single-phase VFD control a three-phase motor?
Yes, it can. Currently, DAT offers a type of single-phase VFD with 220V AC input that can control a three-phase 220V motor.
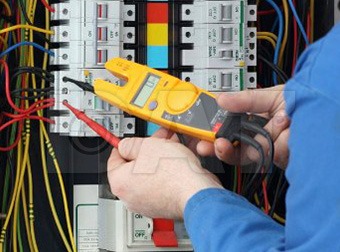
Why does VFD display normally when powered up but trips circuit breaker when running?
Typically, this occurs due to a short circuit in the output phases of VFD. Please carefully inspect and contact the supplier for the best support. Check for any grounding faults; if present, address them before running the inverter. If intermittent tripping occurs, and there is a considerable distance between VFD and motor, consider adding an ... Read moreQ&A
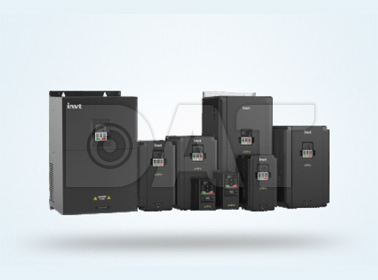
Why does motor connected to VFD run very hot?
Causes Incorrect motor settings. Incorrect motor wiring. Running motor at a frequency too low (below 30 Hz). How to troubleshoot Carefully review motor specifications on label and reconfigure them. Double-check motor wiring and ensure that supplied voltage from VFD is correct. Increase running frequency of motor. It may be necessary to adjust the mechanical transmission ... Read moreQ&A
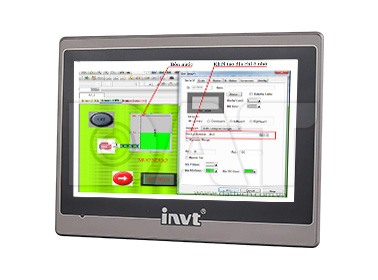
Guide on Creating a Level Shift Simulation in Tank via HMI Display
How to represent the level shift of tank as an analog signal on screen? With INVT’s VT designer software, there is support for the ‘Bar Graph’ tool and a Macro program segment that will help make the simulation of an analog signal, specifically the tank’s level shift signal, as close to reality as possible. Here ... Read moreQ&A
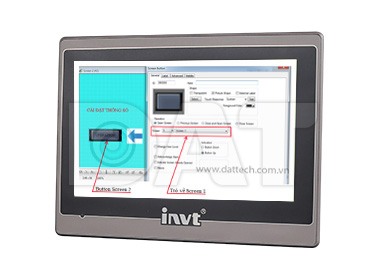
Guide on how to create a flowing effect in a simulated pipeline on HMI display screen
One hypothesis that arises is: If an industrial system has many pipelines: oil pipelines, water pipelines, ventilation ducts, smoke pipes, etc., how can we differentiate between these pipelines? And at what point is each pipeline in operation? When does movement of object inside pipeline start and end? INVT’s VT Designer software supports a method to ... Read moreQ&A
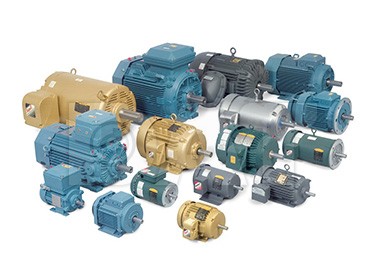
Performing automatic motor parameter detection function for GD35 VFD (MOTOR PARAMETERS AUTOTUNING)
After connecting the power section and completing encoder setup, Autotuning with GD35 is carried out with following steps: Step 1: Reset all settings to default by setting P00.18=1. Step 2: Set P00.03 (Max Frequency) and P00.04 (Upper Frequency Limit). Set these two parameters equal to or greater than rated frequency indicated on motor label. If ... Read moreQ&A